Deck building requires planning and preparation. Before you begin, check with your local building inspection office to see if there are any restrictions or requirements.
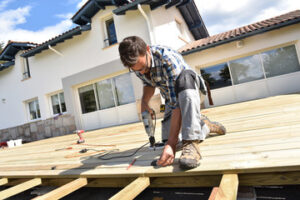
Most home improvement books recommend plotting footing locations with batter boards and string. However, it’s easier and faster to build a layout frame from deck boards or joists. This frame also provides a solid guide for marking and aligning post bases. Contact Deck Builder Stafford for professional help.
Choosing the right materials and hiring professional builders can significantly impact the cost of deck building. It’s also important to factor in the cost of any add-ons or customizations, as well as the price of labor. Many of these factors vary widely depending on the size, design, location, construction materials and any functional add-ons you want to include. For example, adding a pergola or hot tub can increase the overall cost of the project by up to 10%.
The first step in building a new deck is to prepare the area for construction. A contractor will typically remove any existing vegetation and grade the land to ensure a stable foundation. They may also install a waterproofing membrane and a gravel base to ensure proper drainage.
In addition, they’ll use a ledger board, which will be anchored to the house framing. This will require removing the siding where the board must go, and they’ll tuck flashing under the remaining piece of siding. This will prevent water from getting behind the deck framing.
Finally, they’ll install the deck posts. This process can be particularly challenging if you live in an area with cold climates, as frost heave is a common problem. To avoid this, it’s normally recommended that you install the deck posts 4 or 5 feet below ground level to protect them from the freezing and thawing cycles of winter.
Labor costs vary widely depending on the geographic location and local market rates for construction services. They’ll also depend on how complex the design is and if it requires second-story decks or unique add-ons. In addition, a permit may be required, which will add to the overall labor cost.
Materials
A deck’s design and materials determine its performance and durability. Choosing the right material can make or break your budget. Depending on the cost of the materials used, you may have to limit your deck’s features or find other ways to cut costs.
The frame of a deck is usually made from pressure-treated lumber such as pine, fir or spruce. It supports the planks that make up the rest of the structure. The planks can be wood, plastic or a composite material that blends waste wood fibers with recycled plastic.
Wood can be stained or painted to complement the landscape or match a home’s color palette. Cedar is a popular choice for its natural resistance to insects and rot. However, it is prone to moisture damage and requires regular sanding and staining to maintain its beauty. Cedar is also vulnerable to splinters.
Hardwoods like Ipe, Cumaru or Garapa are also an option for decking. While they are more expensive than softwoods, they are very dense and have a natural resistance to rot and insect infestation. They require extra handling and special hardware to install. Hardwoods are more durable than softwoods but they can be difficult to work with and are prone to cracking and splitting.
Some homeowners choose to use composite or capped composite decking for the surface of their decks. These materials are made from a blend of recycled plastic and wood fibers and are available in a wide range of natural-looking hues and grain patterns. They are barefoot friendly and heat resistant but can absorb water causing mildew. They are also more expensive than wood but over time they may pay for themselves through their longevity.
Design
Decks are often kept under lock and key, due to copyright concerns or competition, but if you’re lucky enough to work in a studio, it’s a good idea to ask older freelancers for some examples of their previous work. If not, there are plenty of online resources you can check out to see what other creatives are doing with their decks.
Once you’ve got a feel for the design of your deck, you can start planning the details. Your budget will play a major role in the overall scope of your deck, and it’s important to be realistic about what you can afford. You can use a deck design tool to compare prices on different components and view estimated costs with and without labor factored in.
A footing is a concrete slab that’s laid on the ground, and it supports the posts that carry the load of your deck. The number of footings will depend on your site, and you should consult a building department to learn about frost depth requirements in your area.
Besides the foundation, the ledger board is another crucial component of a deck. This board is anchored to the house framing by using joist hangers and forms the structural side of the deck against your home. To install a ledger board, first remove the siding to expose the area where it must go. Then, tuck flashing under the piece of siding that remains above this area and extend it down the side of your home to prevent water from getting behind the framing.
To make your deck more functional, you can also add railing and stair lighting. These features are particularly helpful if you plan on entertaining after dark. Additionally, adding plants and greenery can visually separate areas of your deck and make it more inviting.
Installation
When building a deck, it is important to follow the right installation steps. A mistake during the foundation process could compromise the structure of your entire deck and lead to premature structural failure. To avoid this, always take your time and make sure you have a clear understanding of the process.
The foundation of a deck is built using concrete piers that are driven into the ground to help spread the load over a larger area. The piers should be at least as deep as the frost line, which varies geographically. If you’re unsure of how to dig the hole for the piers, consult your local building department for information on how deep to go.
Once the footings are in place, a ledger board is attached to the house and the joists are framed out. Be sure to use pressure-treated lumber for this step. If you don’t, it will rot quickly. Then, a shear stud (also called a Nelson stud) is inserted on each low point of the beam, which will prevent the shear from bending and cracking.
After the frame is erected, joist hangers are fitted to the ends of each side joist and fastened to the ledger with 16d nails. Next, the joists are cut and fit to each other to form the deck floor. The joists should be staggered to avoid butt joints and to create a more appealing deck.
A fascia is then installed to conceal the joists and hardware with more attractive material. Be sure to measure carefully to ensure that all boards are straight, and that the gap is uniformly spaced. April suggests using a screw placement guide to maintain consistent screw placement, as well as using stainless steel screws over galvanized ones to avoid black streaks and to increase longevity.
Maintenance
When a deck is finished, it needs routine care to keep it looking good and functioning properly. Cleaning, staining and sealing, repairing damaged boards, and splinter-free railings are all important maintenance tasks. Regular inspections will help to spot problems and prevent them from escalating into major issues.
The deck joists and handrails should be checked for signs of wood rot and other structural problems. These should be repaired immediately to protect the safety of people using the deck. It is also a good idea to inspect the wood where the deck’s ledger board connects to the house for damage. If the wood is soft or presents water stains, it must be replaced.
It is a good idea to replace any loose or splintered boards as well. This will prevent the wood from further splitting or cracking. Loose nails and screws can become a safety hazard. They should be hammered in or screwed back in place. Deck railings should be able to support the weight of a person standing on them. If a railing is not stable, it should be replaced.
A good time to apply a stain or sealant is in the spring and fall, when the weather is dry. It is a good idea to apply an additional coat after the first year or two of staining or sealing.
Decks that are used frequently should be inspected more often than those that are not. In addition to the usual maintenance, it is a good idea to add a wood preservative to the deck to protect against mildew. A wood preservative can be brushed on, rolled on with a paint roller, or sprayed. If spraying is the method of application, tarps should be put down to protect plants, air conditioners, and other equipment.